Did you know that more than 30% of all building materials delivered to a construction site ends up as waste? The US alone produced more than 600 million tonnes of construction-related waste in 2018. Construction waste is a big problem that affects projects and pollutes the environment.
When proper waste management practices are established, contractors can save money because they will only buy what is required for the project. Construction waste is defined as any material produced as a result of abandoned construction work. This type of waste can include materials from excavation work, demolition, or even refurbishment.
Let’s discuss some of the most common types of construction waste.
Common construction waste in the market
One of the most common types of construction waste is dredging material and asbestos. Dredging materials, such as rocks, tree stumps, and soil are found when excavating a site. Other construction waste types include:
- Bricks
- Glass and plastic
- Metallic waste
- Cement
- Adhesives and sealants

As infrastructure projects increase around the country, construction waste is also expected to increase.
One strategy contractors can use to reduce construction waste is having their companies develop reuse and recycle policies.
Another strategy construction companies can use is avoiding errors. Hiring qualified personnel ensures that there are competent workers who are more likely to read blueprints correctly, reducing the chances of rework.
Project managers can also opt to build green buildings. Green buildings use more reusable materials than perishable ones, with materials that can be reused when the structure is demolished.
7 useful tips for construction waste management
1. Use technology to minimize waste
Modern technology can come in handy when dealing with construction waste management. Contractors can use AI, optioneering, and BIM technology to create prefabricated materials in factories. The prefabricated materials are made with precision accuracy, meaning they will not leave behind waste when assembled on site.
Platforms like ALICE Technologies leverage BIM technology to measure the number of resources required to complete a given project and create 3D and 4D models. Because the platform can accurately estimate how many materials will be needed, post-construction waste is reduced significantly.
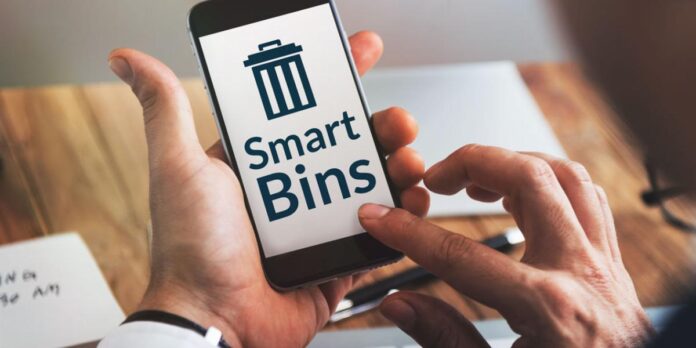
Construction optioneering platforms can be used to simulate complex construction projects. The simulations can be used to identify alternatives or options that can be used to reduce risk and increase the profit margin.
2. Have a detailed construction plan
The benefit of having a detailed construction plan is that you reduce the risk of errors, leading to little material waste. A detailed construction plan should contain the following pieces of information:
- The exact number of materials required
- A recycling policy attached to the plan
- Information about the location of different types of recycling bins
- An education program on how workers can identify and sort waste materials
Create a construction waste management plan including this information. In the long run, contractors will benefit from reduced construction waste, eventually increasing their profit margins.
3. Build materials back into the new structure
Another way that you can reduce construction waste is to reuse materials. For example, you can simply redesign the structure with a remodeling project instead of knocking it down to rebuild a new one. When you have things like wood-framed constructions, instead of throwing them away, you can simply use them as spacers.
4. Segregate waste
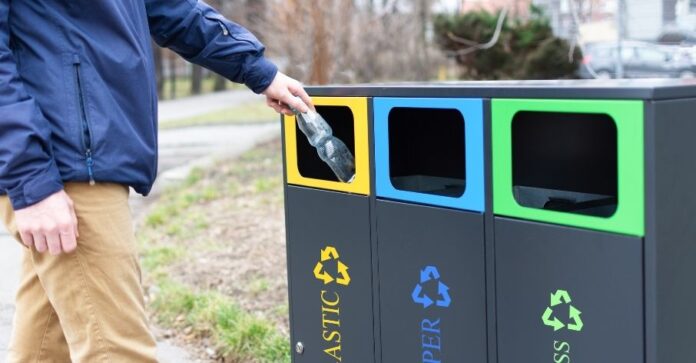
You can manage construction waste by designating a waste segregation area. One main advantage is clearing the construction site of debris and waste. Once all construction waste is taken to the segregation area, it should be separated based on whether they are reusable.
If there is a significant amount of waste, such as blocks and bricks, it is advisable to invest in a mini crusher. The crushed materials should be stored separately for easy disposal. Contractors should ensure that there is a supervisor who will make sure all waste is segregated as it should be.
5. Deconstruct instead of demolish
Let us assume that you’re clearing the site of an old building. In this case, you can either demolish or deconstruct the structure. If you destroy the old building, you reduce the number of materials you can reuse.
However, deconstruction focuses on salvaging reusable materials, and then demolishing the rest. This strategy reduces construction waste. Another thing you need to know is that in some structures, you will need to use a combination of deconstruction and demolition.
6. Build standard structures
One advantage of building a standard structure is that you receive standard supplies. So how is this a benefit? Standard supplies do not have to be cut or adapted because they will fit perfectly in the built structure.
7. Partner with the right company
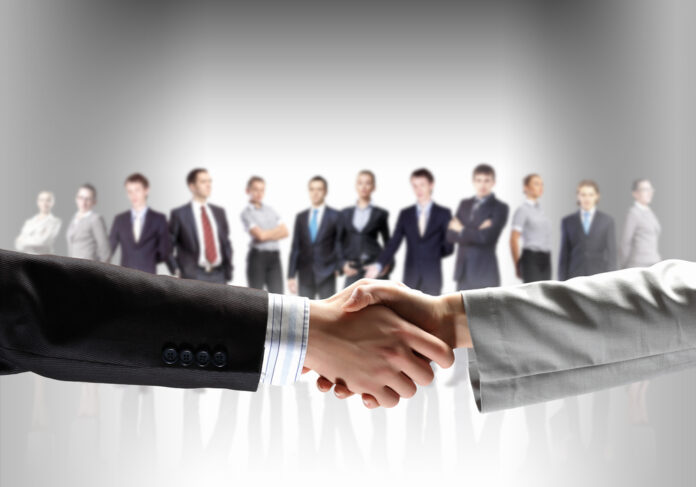
Another effective strategy is to partner with a reputable waste management company. Reputable waste management companies will provide guidelines for sorting and reducing waste. With a reputable company, you’ll need to plan when they will collect your construction waste.
It is also vital to ensure they have the proper equipment for the job. The partner company should have the appropriate tools for its services if you are working on a large construction project. They should, for example, have trucks and tractors to carry excavation waste, such as soil and rocks.
If they do not have the right tools, there is a possibility that the construction site will be left with garbage that ends up obstructing the construction project.
In conclusion, every construction company should have a waste management policy. A waste management policy should be created with input from waste management companies, who can better advise how to reduce and dispose of it.